|
Post by wvengineer on Sept 17, 2015 23:46:26 GMT
Need some help from out HVAC experts. I have a Carrier brand AC/heatpump in my house. Today the compressor would run, but the fan would not. I opened up the internal unit and vacuumed out some dirt from the bottom and probed around the wiring. The fan relay was getting power, but voltage across the fan was low. I turned it off and probed the run capacitor on the fan housing. After that, when I turned it on, the fan was getting correct voltage and it started right up when I reconnected the fan wires.
A year to two ago, I had the same problem and I remember something similar fixed it then.
So what is going on? Is the capacitor going bad? How do I check that it is good? (My multimeter does not have a capacitance setting.)
|
|
|
Post by the light works on Sept 18, 2015 1:33:00 GMT
Need some help from out HVAC experts. I have a Carrier brand AC/heatpump in my house. Today the compressor would run, but the fan would not. I opened up the internal unit and vacuumed out some dirt from the bottom and probed around the wiring. The fan relay was getting power, but voltage across the fan was low. I turned it off and probed the run capacitor on the fan housing. After that, when I turned it on, the fan was getting correct voltage and it started right up when I reconnected the fan wires. A year to two ago, I had the same problem and I remember something similar fixed it then. So what is going on? Is the capacitor going bad? How do I check that it is good? (My multimeter does not have a capacitance setting.) I don't know a really good workaround for testing capacitors. if you have something that runs about a 9V test current, you can at least test for a short in it, but I'm wondering if you are getting a bad connection at the cap, or if you are getting buildup that is shorting across the terminals. (it will show continuity for a while, and then the continuity will drop and finally cut out if it is still functioning at all - but most multimeters don't have enough test voltage to charge it in a reasonable time)
|
|
|
Post by wvengineer on Sept 18, 2015 2:07:20 GMT
I've got a couple 13.7V power supplies. Could those work for a source?
|
|
|
Post by the light works on Sept 18, 2015 4:11:25 GMT
I've got a couple 13.7V power supplies. Could those work for a source? DC? it I think you can use the meter in voltage mode, and it should show the voltage dropping out as the cap charges. of course, it will only show a short or an open fault - it won't show the actual capacitance. my first boss had a discharge lighting tester and it included a cap test function.
|
|
|
Home HVAC
Sept 18, 2015 5:37:14 GMT
via mobile
Post by GTCGreg on Sept 18, 2015 5:37:14 GMT
It really sounds like you just have a bad connection. If the connections are push on spade type connectors, take them off and crimp them down with a pair of pliers or needle nose. If they don't grab the terminals tight, you can get a bad connection and the fan will not run
Fan run capacitors seldom short. If anything they will open circuit. When that happens, you should still read the full line voltage on the fan motor. The fan motor will hum, draw current, and get warm, but will not start turning. If the fan sometimes starts, but is intermittent in doing so, it's usually the sign of a bad run capacitor.
Since you were getting no, or low voltage at the fan motor, I really think your problem is a bad connection.
|
|
|
Post by the light works on Sept 18, 2015 13:47:17 GMT
It really sounds like you just have a bad connection. If the connections are push on spade type connectors, take them off and crimp them down with a pair of pliers or needle nose. If they don't grab the terminals tight, you can get a bad connection and the fan will not run Fan run capacitors seldom short. If anything they will open circuit. When that happens, you should still read the full line voltage on the fan motor. The fan motor will hum, draw current, and get warm, but will not start turning. If the fan sometimes starts, but is intermittent in doing so, it's usually the sign of a bad run capacitor. Since you were getting no, or low voltage at the fan motor, I really think your problem is a bad connection. and the fact that poking at the capacitor fixed it supports that theory. in addition to the mechanical adjustment, there are antioxidant products available for electrical connections. Noalox is the most obnoxious of the lot, so any other product I know of will be preferable, but if noalox is the only option, it is better than nothing.
|
|
|
Post by wvengineer on Sept 18, 2015 22:50:53 GMT
The options for an anti-oxidation compound are limited to what I can find at Lowes since the local Radio Shack closed.* Any recommendation for online sources?
* The only loss there is that I now cannot buy electrical solder in my town.
|
|
|
Post by the light works on Sept 19, 2015 0:11:55 GMT
|
|
|
Post by silverdragon on Sept 20, 2015 11:08:54 GMT
The above advice sort of explains everything I would have said anyway, but, just to add, does the fan motor have a "Star Delta" startup procedure?...
How many wires come back from the fan?.. if its only two, you could probably ignore the below questions. This page sort of explains a little of what I am trying to explain....http://electrical-engineering-portal.com/star-delta-motor-starter However.... see [*] paragraph.
As in, would it have a lower power to start the motor the turn it up to run at full speed once it starts. I know this is usual of larger induction motors, but I also know its sometimes used in smaller quiet-start fans around sensitive equipment....
How to find out.
Run the test with the fan on, and see if the starting power "Jumps" suddenly when the fan has started turning, as in, going from that as you stated....
I would question the "Is the fan running yet" part of the schematics for the fan control, in that the unit may start on low power, get a "Ok I am running" signal from the fan, then switch to high power.
The sensor that triggers the "Ok, I am running" signal may have gotten some dirt on it and you cleaned it out.
[*]However... I also note that some systems do the startup procedure without an "Ok Running" sensor. As in, the control schematic just has a low-power-wait[1]-high-power startup. In that case, your low OR high power capacitor/control may have dry joints.... Check the control circuit boards. If it looks "Simple" ignore what I just dun wroted......
I know, I am getting overly complicated, its just the control schematics for the things I used to play with came in Volumes.... A Two volume control was pretty small, and would do a couple of thousand square feet of office space.
I never played with Home sized stuff. Unless you cont the time we did a four double wardrobe sized control board installation for a very expensive london home for some super-rich person.... House larger than some schools.
|
|
|
Post by the light works on Sept 20, 2015 14:10:11 GMT
remember we don't have three phase residential power, here; hence the need for capacitors.
|
|
|
Home HVAC
Sept 20, 2015 18:46:55 GMT
via mobile
Post by GTCGreg on Sept 20, 2015 18:46:55 GMT
remember we don't have three phase residential power, here; hence the need for capacitors. Right. A three phase motor doesn't use a run or start capacitor.
|
|
|
Post by c64 on Nov 29, 2015 14:59:18 GMT
remember we don't have three phase residential power, here; hence the need for capacitors. Right. A three phase motor doesn't use a run or start capacitor. It does if you can't supply it with rotary current. Lawn mowers use 3~ motors but a 5-core cable would by mighty inconvenient so they use a capacitor. Same for most larger fans e.g. kitchen hoods. The alternative is using a frequency converter. They are rather cheap nowadays and they can be used to supply a 3~ motor with only 1~. When the capacitor in my lawnmower broke, I installed a frequency converter I had scavenged in a factory. While the mower has its original RPM, it has a lot more torque so it can handle high grass much better.
|
|
|
Post by c64 on Nov 29, 2015 15:19:44 GMT
Need some help from out HVAC experts. I have a Carrier brand AC/heatpump in my house. Today the compressor would run, but the fan would not. I opened up the internal unit and vacuumed out some dirt from the bottom and probed around the wiring. The fan relay was getting power, but voltage across the fan was low. I turned it off and probed the run capacitor on the fan housing. After that, when I turned it on, the fan was getting correct voltage and it started right up when I reconnected the fan wires. A year to two ago, I had the same problem and I remember something similar fixed it then. So what is going on? Is the capacitor going bad? How do I check that it is good? (My multimeter does not have a capacitance setting.) Even a multimeter with "C" capability won't tell you much about the condition of the capacitor. Buy an inexpensive component tester. You can get this one for less than $20! 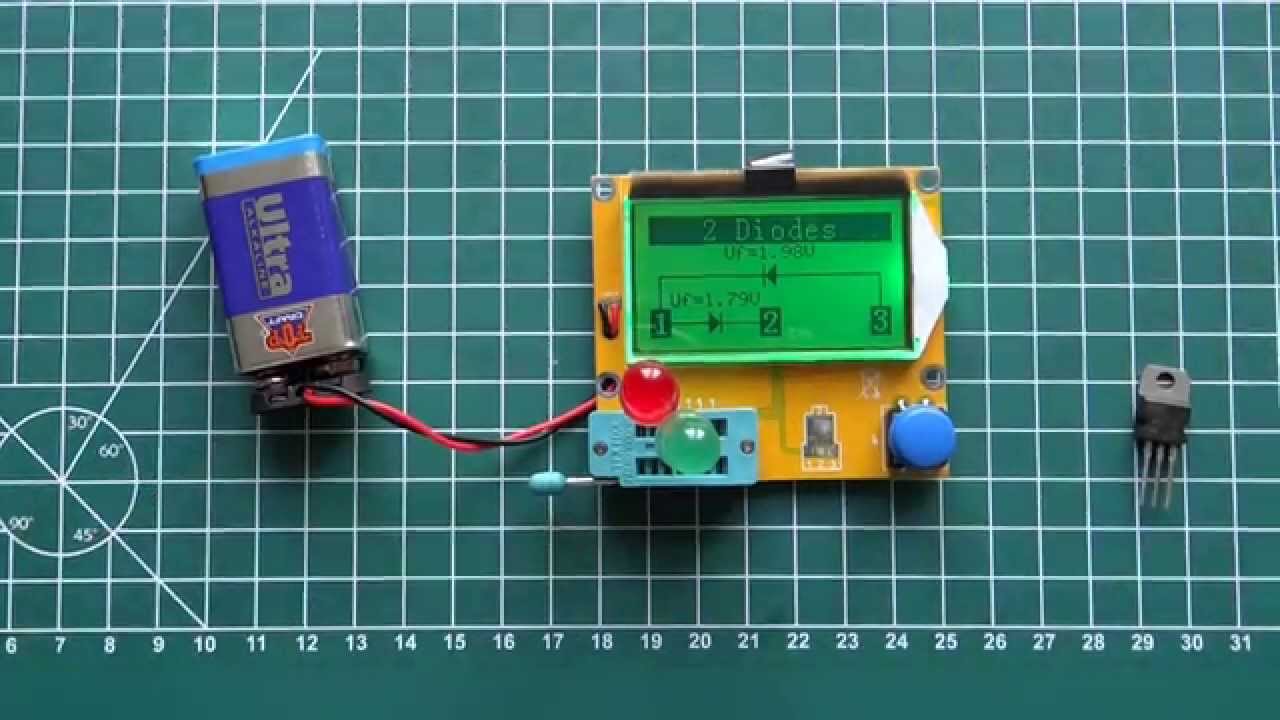 Just make sure to discharge the capacitor by short circuiting it for a minute before you connect it to the tester. The tester will then tell you the capacity, resistance and leakage of the capacitor. Even at full capacitance, if it leaks too much or has to much resistance (in most cases both), it won't delay the phase properly any more and the motor won't get a good enough rotary field in order to spin up. The problem is that due to vibrations, the capacitor can become damaged. Inside, there is a spiral of aluminium foil submerged in the "electrolyte". The fluid causes oxidation so the surface of the aluminium will form an insulation barrier. One terminal is connected to the aluminium and the other one to the conductive electrolyte. The aluminium oxide is what separates the two conductive "plates" of the capacitor. The trick is that the aluminium oxide layer is very thin. The thinner the insulation, the greater the capacity. Also if something breaks, the electrolyte will fix the capacitor by restoring the insulation. So the capacitor will loose some capacity but remains working. From vibrations, the aluminium spiral might touch the casing. By removing the capacitor to examine it, you shake it and this can cause the electrolyte flow in between the spiral and casing and restore the insulation. Also the spiral might cack so the electric path through the spiral is narrowed while it still has its full surface so you have all the capacity but a tremendous resistance in the path of the current. Also the electrolyte will leak out due to temperature changes and the parts of the spiral which are not submerged won't add capacitance any more. So it is best to simply replace the capacitor when in doubt. It might fail a bit later anyway. Or install a frequency converter. Get one which has a control input so the converter stays on and the circuit which used to control the fan will tell the converter what to do. Some even are programmable and come with a temperature probe. This way you can adapt the speed (and noise levels) to the circumstances. The greatest improvement is that a frequency converter can sense dirt or other objects in the fan and will protect the fan motor while sounding an alarm so you know that the fan is down.
|
|
|
Post by the light works on Nov 29, 2015 15:22:31 GMT
Right. A three phase motor doesn't use a run or start capacitor. It does if you can't supply it with rotary current. Lawn mowers use 3~ motors but a 5-core cable would by mighty inconvenient so they use a capacitor. Same for most larger fans e.g. kitchen hoods. The alternative is using a frequency converter. They are rather cheap nowadays and they can be used to supply a 3~ motor with only 1~. When the capacitor in my lawnmower broke, I installed a frequency converter I had scavenged in a factory. While the mower has its original RPM, it has a lot more torque so it can handle high grass much better. here, if they are going to run a motor on single phase, they use a single phase motor. the freq drives I have worked with are a bit big to work on a lawnmower.
|
|
|
Home HVAC
Nov 29, 2015 15:30:21 GMT
via mobile
Post by GTCGreg on Nov 29, 2015 15:30:21 GMT
Right. A three phase motor doesn't use a run or start capacitor. It does if you can't supply it with rotary current. Lawn mowers use 3~ motors but a 5-core cable would by mighty inconvenient so they use a capacitor. Same for most larger fans e.g. kitchen hoods. The alternative is using a frequency converter. They are rather cheap nowadays and they can be used to supply a 3~ motor with only 1~. When the capacitor in my lawnmower broke, I installed a frequency converter I had scavenged in a factory. While the mower has its original RPM, it has a lot more torque so it can handle high grass much better. Most small AC motors that use a capacitor are actually two phase motors. The capacitor is used on a single phase circuit to provide a phase shift for the second winding in the motor. If the motor has two capacitors, it's still a two phase motor. It's just that the larger capacitor is used for starting and then the smaller capacitor to keep it running. Many home appliances are starting to use variable frequency drive for the motors. It's done more for efficiency than anything else.
|
|
|
Post by c64 on Nov 29, 2015 15:31:05 GMT
It does if you can't supply it with rotary current. Lawn mowers use 3~ motors but a 5-core cable would by mighty inconvenient so they use a capacitor. Same for most larger fans e.g. kitchen hoods. The alternative is using a frequency converter. They are rather cheap nowadays and they can be used to supply a 3~ motor with only 1~. When the capacitor in my lawnmower broke, I installed a frequency converter I had scavenged in a factory. While the mower has its original RPM, it has a lot more torque so it can handle high grass much better. here, if they are going to run a motor on single phase, they use a single phase motor. the freq drives I have worked with are a bit big to work on a lawnmower. Single phased motors either need brushes so they wear out much quicker and require maintenance or they are very inefficient. There are modern 1~ motors but they either are in fact brush-less DC (with built in electronics) or classic 3~ with a miniature capacitor "hidden" inside.
|
|
|
Post by the light works on Nov 29, 2015 15:43:02 GMT
It does if you can't supply it with rotary current. Lawn mowers use 3~ motors but a 5-core cable would by mighty inconvenient so they use a capacitor. Same for most larger fans e.g. kitchen hoods. The alternative is using a frequency converter. They are rather cheap nowadays and they can be used to supply a 3~ motor with only 1~. When the capacitor in my lawnmower broke, I installed a frequency converter I had scavenged in a factory. While the mower has its original RPM, it has a lot more torque so it can handle high grass much better. Most small AC motors that use a capacitor are actually two phase motors. The capacitor is used on a single phase circuit to provide a phase shift for the second winding in the motor. If the motor has two capacitors, it's still a two phase motor. It's just that the larger capacitor is used for starting and then the smaller capacitor to keep it running. Many home appliances are starting to use variable frequency drive for the motors. It's done more for efficiency than anything else. I've seen appliances with multispeed motors, but most of them are multiwinding motors. the controller just energizes the set of windings they want. but yes, a single phase motor has the windings arranged so the lagging current from the capacitor causes the torque. the alternative is the shaded pole motors which simply interfere with the magnetic field on one side of the armature.
|
|
|
Post by c64 on Nov 29, 2015 15:44:21 GMT
It does if you can't supply it with rotary current. Lawn mowers use 3~ motors but a 5-core cable would by mighty inconvenient so they use a capacitor. Same for most larger fans e.g. kitchen hoods. The alternative is using a frequency converter. They are rather cheap nowadays and they can be used to supply a 3~ motor with only 1~. When the capacitor in my lawnmower broke, I installed a frequency converter I had scavenged in a factory. While the mower has its original RPM, it has a lot more torque so it can handle high grass much better. Most small AC motors that use a capacitor are actually two phase motors. The capacitor is used on a single phase circuit to provide a phase shift for the second winding in the motor. If the motor has two capacitors, it's still a two phase motor. It's just that the larger capacitor is used for starting and then the smaller capacitor to keep it running. Many home appliances are starting to use variable frequency drive for the motors. It's done more for efficiency than anything else. I have never seen a 2~ motor over here. All 230/400V motors are either true 1~, DC (with rectifier), true 3~ running on 3~ or 3~ on "Steinmetz".  This is the common Steinmetz circuit. The switch is to reverse the direction of the motor. Most motors have the capacitor connected between N and V₁/U₂ permanently if they are not meant to run "backwards". The second capacitor (in parallel, usually with timed switch) is meant to boost torque at low RPM so the motor has more power to spin up but has to be disconnected for full RPM. Pumps and compressors usually use a bypass instead, once the motor had spun up, the bypass is disabled so the motor can spin up with a lot less load on it.
|
|
|
Post by the light works on Nov 29, 2015 15:47:28 GMT
here, if they are going to run a motor on single phase, they use a single phase motor. the freq drives I have worked with are a bit big to work on a lawnmower. Single phased motors either need brushes so they wear out much quicker and require maintenance or they are very inefficient. There are modern 1~ motors but they either are in fact brush-less DC (with built in electronics) or classic 3~ with a miniature capacitor "hidden" inside. I'm familiar with the ones that have the miniature capacitor "hidden" inside. when the capacitor overheats and blows, the motor is worthless. I prefer the US models which use a single phase motor for a single phase motor.
|
|
|
Post by the light works on Nov 29, 2015 15:51:48 GMT
here is how ours are made:  or more precisely like this - note the capacitor is outside the housing where it is replaceable. 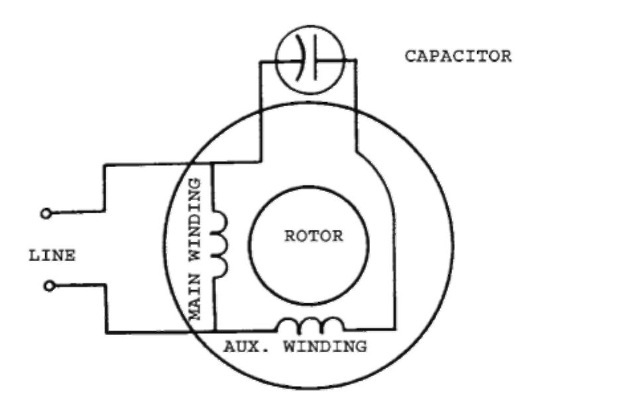
|
|